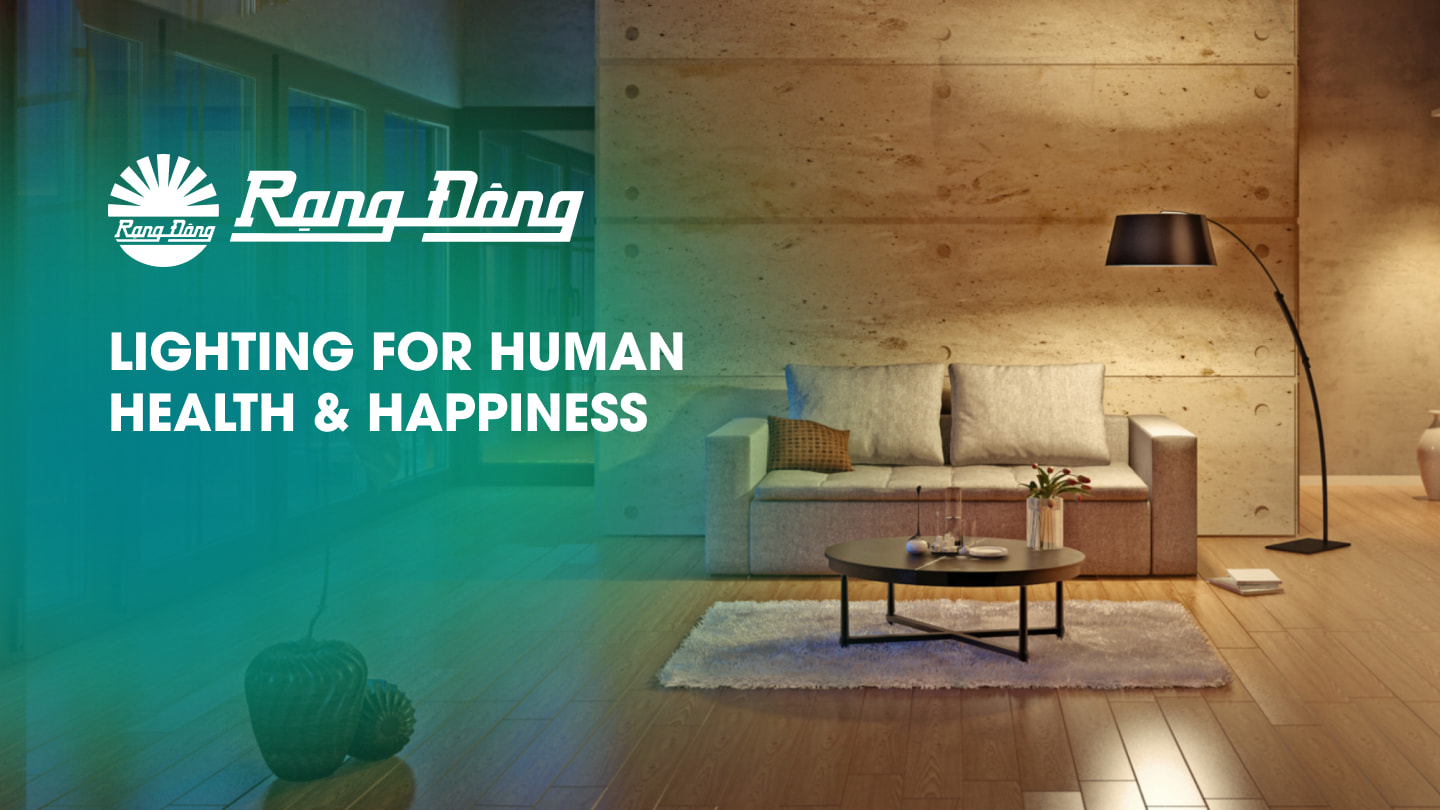
Overview of a SMT production line
Every lighting manufacturer shall have in place several SMT production lines as parts of lighting production. Their quality partially determines the luminous flux and reliability of the final lighting products. They are set up at the first stage in the whole lighting production. The following article provides details on the role of the SMT production line.
SMT production line
SMT is the abbreviation of “surface mount technology”, is a method in which the electronic components are mounted directly onto the surface of a printed circuit board (PCB).
Developed in the 1960s, SMT has been applied widely in electronics to fabricate electronic boards in various devices. The accuracy and sophistication of SMT has been improved and therefore, enabling manufacturers to make micro-scale electronic components, and micro-electronic boards.
In the lighting industry, LED modules are always the SMT PCBs and Driver modules, including both SMT and through hole technology (THT) components. The photo below shows parts of an LED SMT PCB and a driver PCB.
SMT can be imagined simply like the way above
A SMT LED module (left) and SMT components attached to a driver PCB (right)
The difference between SMT technology and THT technology
Both the technologies share a common task: connecting electronic components directly to the printed circuit board (PCB).
But how they are connected makes their difference. SMT connects by mounting surfaces of components onto the PCB copper pads. Meanwhile, THT connects by soldering component pins to the PCB holes.
Nowadays, SMT LED packages show their advantages against the THT LED packages. Therefore, LED PCBs are totally made on SMT production lines and used widely in lighting products.
Illustration of through hole technology in which component pins are soldered to PCB holes
However, the Driver board must include both THT and SMT components, since the features of the Driver board are much different from those of LED modules. The circuit design as well as the distribution of components on the Driver PCB are much more difficult than those on LED PCB.
Normally, we only use one kind of SMT LED chip, but to make a lighting driver, we have to use many different components like capacitors, resistors, transistors, varistors, inductors, ICs, etc. They can be either SMT or THT components. Thus, SMT and THT applied for Driver PCB are more complicated than those for LED PCB.
THT resistor, and THT diode are through-hole soldered on the Driver PCB
Operation of a SMT production line
A SMT production line normally includes 5 parts: loader, stencil machine, pick and place machine, reflow oven and finished PCBs.
Structure of SMT production line
Firstly, PCBs go through the loader to the stencil machine where solder cream is applied. The pick and place machine will feed LED packages in the right positions of the solder pads on PCBs. Next, PCB sets with SMT components will be checked by workers to see if there is any missing SMT component or any deviate position on the PCB. Any defect spotted means the faulted part being removed for correction.
Next, the passed PCBs will go through the reflow oven, which incorporates nine heat zones and three cooling zones. The heat melts the solder cream to connect the SMT component surface with copper pads of PCBs. The cooling zones help harden the soler pads. Finally, the PCBs go out of the oven and workers will check the PCB appearance before automated optical inspection and lighting checks.
Worker is operating a SMT production line
Most stages in the modern SMT production line are operated automatically. Therefore, currently a SMT production line is capable of making an impressive output, turning out about 60,000 SMT components per hour.
Should you have any questions, wish to share your ideas of flasks, or request a quotation, please send us an email to: export@rangdong.com.vn
Our website: https://en.rangdong.com.vn/