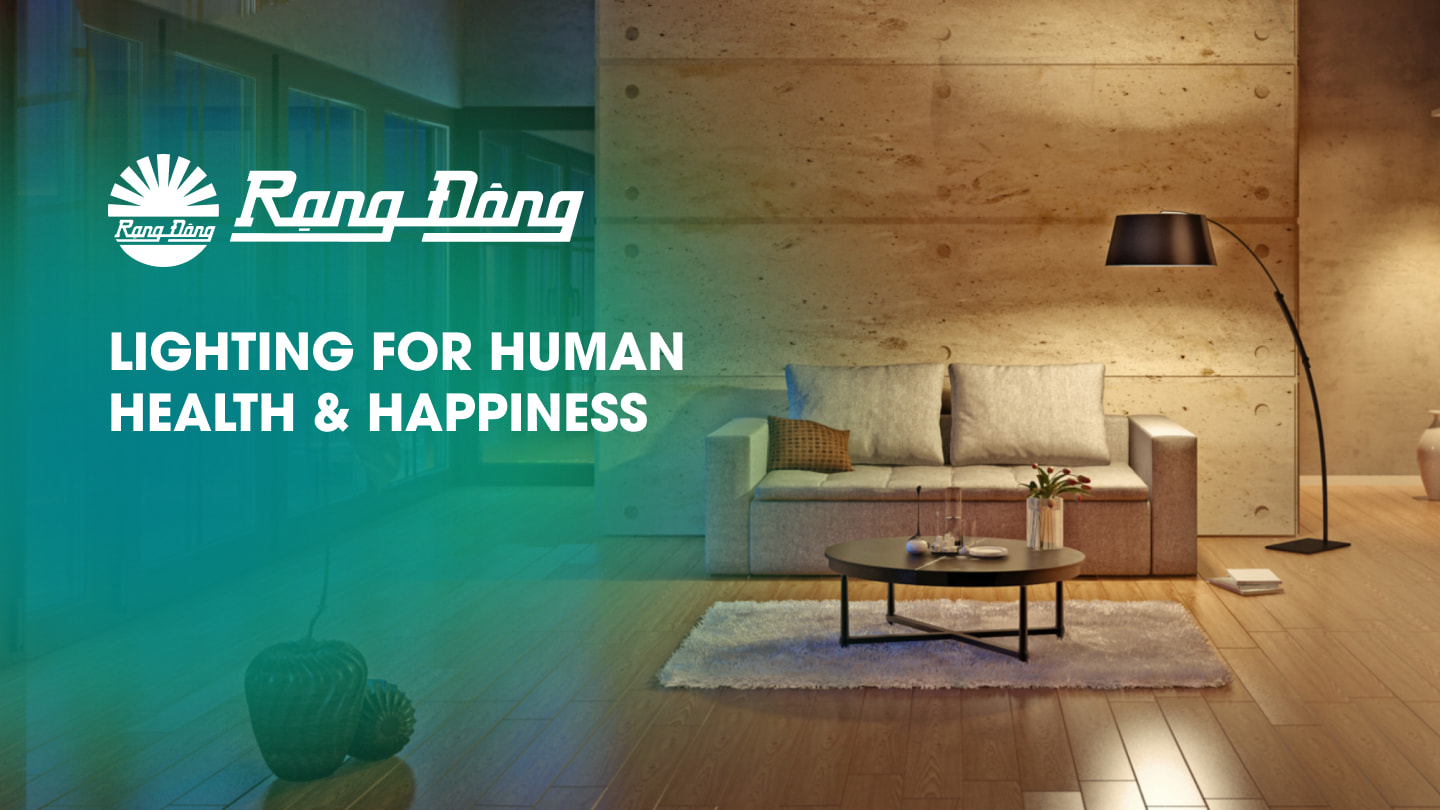
Vietnam's Rang Dong makes LED Tube production line a core part
Rang Dong has been observing the mercury-free principle in its standard LED production process as part of the company's tasks to bring high efficiency and high quality to LED Tube production line while protecting the environment.
LED Glass Tube Semi-automatic Assembly Line
The Hanoi-based company, fully known as Rang Dong Light Source and Vacuum Flask Joint Stock Company, has a long history of continuous development since its 1961 establishment.
It carefully selects components and runs thorough tests to ensure the best quality for its LED tubes so they could fully meet consumers' expectation.
We are going to take a closer look at Rang Dong's LED Tube production line. The company makes glass tubes at a factory in Hanoi's northern neighboring province of Bac Ninh. The tubes then are transported back to Hanoi's facility for assembly. Rang Dong's LED Tube production lines contains the following stages. In the first stage, LED modules are separated, then glued by an automatic sub-platter glue machine before being stuck to the glass tube.
- The glass tubes are left for 2 hours for the glue to dry.
- After the glue is dried, tubes are taken into the line.
At the start of the assembly line, glass tubes are placed on the conveyor belt in a way to balance their position.
In the next stage, AC wire is soldered to one end of the tube, while the power source is attached to the other end.
- An automatic welding machine is in use at this stage.
- For attaching the power source, workers do it manually, wearing protective gloves and anti-static rings.
After the power source is attached, the automatic welding machines will stick the source welding points together. At this stage, a worker will check and correct if any defect is found on the soldered pads.
The glass tube is picked for the next stage where the tube head is inserted:
- Workers insert the tube head manually via the tube end attached to the power source;
- At the other end with the soldered AC wire stands an automatic tube inserting machine. The tube heads are fed automatically by stacker.
The machine automatically pushes the end cap of the glass tube, helping reinforce the connection of the power cord with the battery.
Now lighting is checked for the first time. Any product with defect is removed for re-checking. The products that have passed the first light inspection are picked up automatically from the assembly conveyor belt and fed to the testing machine. One round of the machine runs for 30 minutes.
Having run the cycle at the testing machine, the tube is picked and taken to the seal printing stage and the second lighting check. Workers would visually check the tubes for errors and remove any of them with errors. Those meeting the standards are placed into troughs for packing in boxes.
Automatic packaging process:
- Paper rolls are run through the line, having product information printed on it. The roll is later cut as per the product's size requirements.
- The tubes are then loaded and packed automatically.
Rang Dong's assembly line has a daily output of 11,000 LED glass tubes and the company has been operating two such assembly lines for glass tubes.
For more details, readers can refer to the video of the LED Tube production line here.
One of the first 13 factories established in Vietnam's northern region in the early 1960s, Rang Dong has continuously grown in both quality and quantity. The country's leading manufacturer of LED products and provider of smart lighting solutions has targeted to become a billion dollar company by 2030, a five-fold increase from around USD 200 million in 2020 revenues.
Should you have any questions, wish to share your ideas of lighting, or request a quotation, please send us an email: to export@rangdong.com.vn.
Our website: en.rangdong.com.vn.